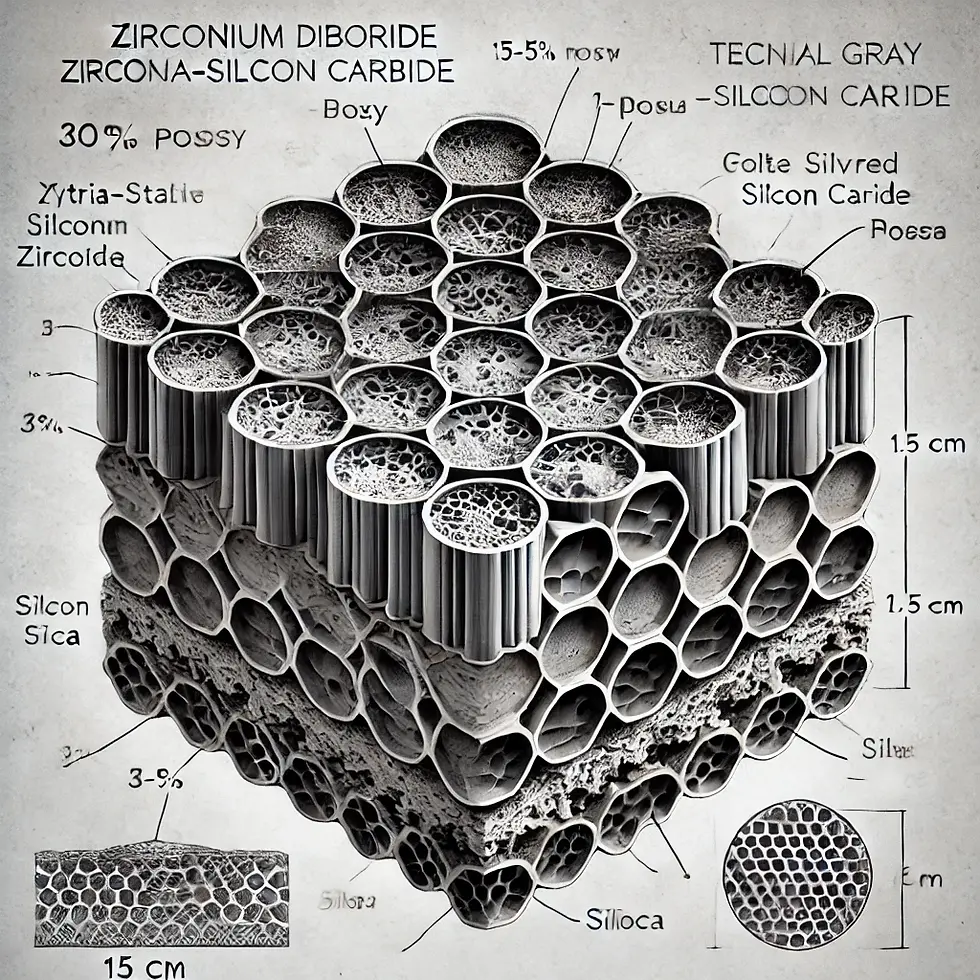
Self-regulating Phase-change Ceramic Tiles for Starship Heat Shield
Self-regulating Phase-change Ceramic Tiles for Starship Heat Shield
Proposal: Self-regulating Phase-change Ceramic Tiles for Starship Heat Shield
Executive Summary
SpaceX’s Starship demands a thermal protection system (TPS) that survives dozens of reentries without frequent replacement, a challenge unmet by current ceramic tiles. We propose a revolutionary tile: a porous zirconium diboride-silicon carbide (ZrB₂-SiC) composite with embedded phase-change material (PCM) microchannels and a self-healing yttria-stabilized zirconia (YSZ) coating. This design actively rejects heat, repairs damage, and targets:
20-30 reentry cycles with minimal maintenance.
50-70% heat flux rejection via PCM melting and vaporization.
Rapid turnaround through reusable PCM and crack sealing.
Scalable production using 3D printing and plasma spraying.
Initial prototyping costs $200k, scaling to ~$50-$150/tile—outpacing current tiles’ lifecycle costs ($50k-$100k/flight) with 50-80% savings over 20 missions. We seek SpaceX’s partnership to test and deploy this game-changing TPS.
Background
Starship’s current heat shield—hexagonal ceramic tiles (likely alumina or silica-based)—handles reentry’s punishing conditions (1,500°C, 1 MW/m²) but requires ~10-15% replacement per flight due to cracking and ablation. Elon Musk has highlighted this as a reusability bottleneck, driving costs ($50k-$100k/flight) and slowing mission cadence. Our solution reimagines TPS as an active, self-sustaining system, leveraging ultra-tough ceramics, phase-change cooling, and self-healing to push Starship toward weekly flights.
Proposed Solution: Self-Regulating PCM Tile Design
Key Features
Substrate:
Porous ZrB₂-SiC composite (30-40% porosity) with interconnected microchannels (10-50 μm).
Why: ZrB₂’s >3,000°C melting point and SiC’s toughness exceed alumina’s limits.
Phase-Change Cooling:
Encapsulated sodium (melting ~98°C, vaporization ~883°C) in microchannels.
Mechanism: Melts at 100°C (absorbing ~400 kJ/kg), flows to surface, vaporizes (2,300 kJ/kg), rejecting heat into the plasma layer.
Reusability: Re-solidifies post-flight, refillable via capillary action or ground injection.
Self-Healing Coating:
100 μm YSZ doped with silicon (Si), applied via plasma spraying.
Mechanism: At >1,200°C, Si oxidizes to SiO₂, sealing microcracks as a glassy phase.
Fabrication:
3D-printed ZrB₂-SiC with microchannels, PCM injected under inert atmosphere, YSZ-Si coating sprayed.
How It Works
Reentry: Heat melts PCM, absorbing energy. Molten sodium flows through channels, vaporizing at the surface to expel ~50-70% of incoming heat flux. YSZ-Si seals cracks in real-time.
Post-Flight: PCM re-solidifies; tile resets with minimal ground intervention.
Outcome: Surface temp drops to ~1,100-1,350°C (vs. ~1,650°C), internals stay <1,000°C, targeting 20-30 cycles.
Technical Advantages Over Current Tiles
Heat Rejection:
Current: ~10-20% flux mitigated via ablation/radiation.
New: 50-70% rejected via PCM (0.1-0.2 g/cm²), reducing thermal load by 300-500°C.
Durability:
Current: ~10 cycles, 10-15% failure rate.
New: 20-30 cycles via self-healing and tougher ZrB₂-SiC.
Reusability:
Current: Frequent swaps (days-weeks).
New: PCM refill in hours, ~5% replacement rate.
Weight:
Current: ~1-2 kg/tile.
New: ~1.5-2 kg/tile, offset by longevity and potential size optimization.
Development Plan
Phase 1: Prototype Development (3-6 Months, $200k)
Objective: Build and test a 5 cm x 5 cm tile for heat rejection and self-healing.
Steps:
3D-print ZrB₂-SiC with microchannels.
Inject sodium PCM, cap with porous plugs.
Apply YSZ-Si coating via plasma spraying.
Testing:
Heat flux test (blowtorch, ~1,500°C, 60 sec).
PCM performance (temp drop, vaporization rate).
Crack healing (SEM post-cycle).
Deliverable: Data vs. current SpaceX tile.
Phase 2: Scale-Up and Flight Test (6-12 Months, $1M-$2M)
Objective: Produce 15 cm tiles for Starship integration.
Steps:
Scale 3D printing to ~100 tiles/day.
Fabricate 50-100 tiles.
Integrate into Starship test flight (e.g., SN25).
Testing: Onboard sensors for temp, durability; post-flight inspection.
Deliverable: Flight-proven tile design.
Phase 3: Production Ramp-Up (12-24 Months, $5M-$15M)
Objective: Achieve 1,000+ tiles/month.
Steps:
Automate 3D printing and PCM injection.
Target ~$50-$150/tile via scale.
Deliverable: Full Starship TPS solution.
Business Case
Cost Savings:
Current: ~$50-$100/tile, ~$50k-$100k/flight (10-15% swaps).
New: ~$50-$150/tile, ~$10k-$20k/flight (5% swaps, PCM refill ~$1/tile).
20-mission savings: ~$200k-$400k vs. ~$1M-$2M—a 50-80% reduction.
Turnaround: Hours to refill PCM vs. days-weeks for tile replacement.
Scalability: Supports 100+ flights/year with minimal refurbishment.
Innovation: Patentable TPS could dominate aerospace.
Risks and Mitigation
PCM Depletion: Vaporization loses ~10-20% PCM per flight.
Mitigation: Refill on ground; test higher-melting PCM (e.g., lithium) for retention.
Weight Penalty: ~10-20% heavier than current tiles.
Mitigation: Optimize porosity, reduce thickness if cooling excels.
Unproven Tech: Self-healing and PCM untested in TPS.
Mitigation: Phase 1 validates concept; fallback to current tiles if needed.
Collaboration Request
We propose SpaceX partner with us to:
Fund Phase 1: $200k for prototype and lab testing (use SpaceX’s plasma rigs).
Provide Expertise: Materials team to refine ZrB₂-SiC and PCM integration.
Flight Test: Equip 50-100 tiles on a Starship mission.
SpaceX gains a TPS that could cut costs by millions and enable weekly flights. We’re open to IP licensing or joint development.
Power in Numbers
30
Programs
50
Locations
200
Volunteers
Project Gallery
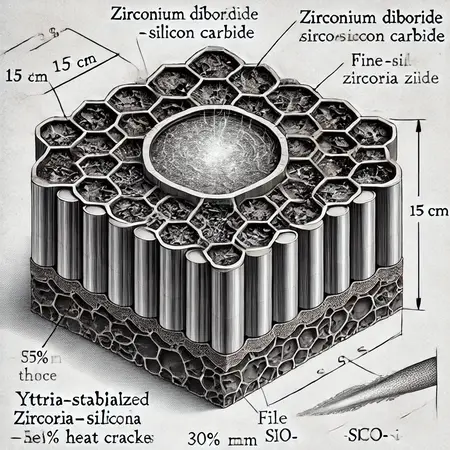